Chanel investiert viel in die Produktion seiner Uhrensparte. Um die Qualität und das spezielle Design seiner Uhren und Werke selbst in der Hand zu haben, setzt die Marke seit Jahren auf ihre eigene Manufaktur in La Chaux-de-Fonds. Jetzt öffneten sich nach langer Zeit wieder einmal die Tore für einen exklusiven Besuch – und was ich dort alles sah, übertraf meine Erwartungen deutlich.
Zugegeben: Chanel ist gemeinhin nicht die erste Marke, an die man als Uhrenfan denkt. Trotzdem war ich immer schon fasziniert von Chanel. Besser gesagt: nicht „immer schon“, sondern seit der Einführung der J12. Oder, noch genauer: seit ich die J12 zum ersten Mal in Händen hielt. Das muss Anfang oder Mitte der Nullerjahre gewesen sein. Es war zum einen das Material, das mich begeisterte. Diese glasartige Härte und Glätte der polierten Keramik, die am Handgelenk so schnell warm wird, dass sie gar nicht mehr hart erscheint. Zum anderen war es die Form. Keine eindeutige Damenuhr, wie man das vielleicht von einer der größten Modemarken des Planeten erwartet hätte, sondern eine Uhr, die man auch als Mann jederzeit und überall tragen kann, ohne Wenn und Aber. Eine Form, dank derer die Keramik ihre optischen und haptischen Reize voll ausspielen kann, was nicht zuletzt am Gliederarmband liegt. Für mich hat Chanel erst mit der J12 so richtig die Welt der Armbanduhren betreten. Und heute ist die Marke daraus nicht mehr wegzudenken.
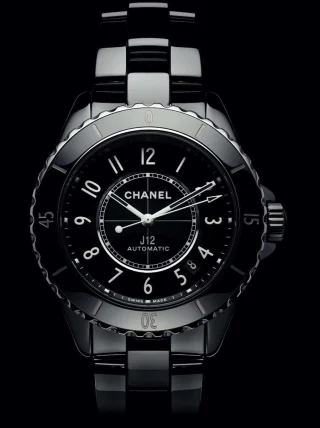
Chanel-Uhren seit 1987
Die J12 fasziniert mich, aber nicht nur sie: Mir hat stets imponiert, wie konsequent und ernsthaft Chanel das Thema Uhr angegangen ist. Nur sechs Jahre, nachdem die Marke 1987 mit der achteckigen Première (HIER geht es zur neuesten Première von 2023) ihren ersten Zeitmesser lanciert hatte, übernahm sie 1993 die Uhrenproduktionsstätte G&F Châtelain in La Chaux-de-Fonds. Das 1947 gegründete Unternehmen hatte sich unter anderem auf das Polieren und Finissieren von Goldkomponenten, die Herstellung von Metallarmbändern und das Setzen von Edelsteinen spezialisiert und für Chanel bereits die Première gefertigt. 1997 baute Chanel ein 8.000 Quadratmeter umfassendes neues Gebäude am Rand von La Chaux-de-Fonds, in das G&F Châtelain einzog – in unmittelbarer Nachbarschaft zum Zeigerhersteller Universo und zur Breitling Chronométrie. Auch wenn G&F Châtelain bis heute seinen Namen trägt und auch Produkte an fremde Uhrenmarken liefert, ist das hier vor allem der Sitz der Chanel-Manufaktur. Die Fläche hat sich fast verdoppelt, seit der Komplex 2012 um ein zweites Gebäude ergänzt wurde, in dem heute ein großer Teil der Schmuckproduktion der Marke stattfindet. Die Chanel-Manufaktur zu besuchen, stand schon lange auf meinem Plan, nicht zuletzt wegen der Fertigung der Keramikgehäuse und -bänder – etwas, das man nicht oft zu sehen bekommt. Jetzt ergab sich endlich die Gelegenheit.Die Chanel-Manufaktur
Zuerst: G&F Châtelain ist gewaltiger, als ich gedacht hatte. Es handelt sich um eine voll ausgestattete Uhrenmanufaktur mit einer überraschend hohen Fertigungstiefe. Auf 14.000 Quadratmetern arbeiten 500 Mitarbeiterinnen und Mitarbeiter, von denen die meisten bereits seit mindestens zehn Jahren im Unternehmen sind. Das heißt nicht, dass 100 Prozent der Produktion hier stattfinden; bekanntlich hat sich Chanel 2019 mit 20 Prozent bei der mehrheitlich von Tudor gehaltenen Werkeschmiede Kenissi eingekauft. Dort werden die Kaliber 12.1 und 12.2 gebaut, die in vielen J12-Modellen ticken. Doch entwickelt und montiert Chanel in seiner Manufaktur die Werke mit Komplikationen – und die Uhren – selbst. Hier werden auch Gehäuse und Armbänder produziert, vor allem die aus Keramik. Eine sehr wichtige Rolle spielt das Setzen von Diamanten. Und dann gibt es immer wieder Qualitätstests. Die hausinterne Folterkammer firmiert unter der Bezeichnung Atelier für Homologation, und in ihr starten wir unseren Rundgang.Der Chefdesigner
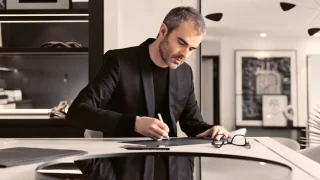
Doch bevor wir eintreten, werden unsere Gedanken weggelenkt von G&F Châtelain, weg von La Chaux-de-Fonds, weg von der Schweiz. Chanel ist eine der größten Modemarken der Welt, da verwundert es nicht, dass die Technik der Uhren zwar sehr wichtig, aber nicht das Wichtigste ist. Über allem thront das Design. Chanels Markenwelt ist grundsätzlich schwarz-weiß und verfügt darüber hinaus über weitere Designcodes, die auch bei manchen Uhren zum Tragen kommen, wie die Farbe Rot, die Legierung Beigegold oder der Löwe, das Sternzeichen von Gründerin Coco Chanel. Herr über Kreativität und Konsistenz ist heutzutage Chanels Uhren-Chefdesigner Arnaud Chastaignt, der sein Büro im Chanel-Kreativstudio an der Place Vendôme in Paris hat. Jede Chanel-Uhr startet mit einer Idee von Chastaignt. Er sendet seine Vorstellungen und Vorgaben nach La Chaux-de-Fonds, und dort setzt man sie in konkrete technische Lösungen um.
Das Technische Büro
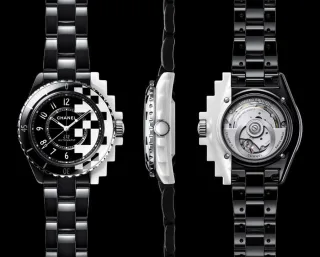
Der Lebenszyklus einer Uhr beginnt in der Entwicklungsabteilung, dem Technischen Büro, in dem etwa 30 Personen arbeiten. Am Beispiel der J12 Hyper Cybernetic erfahre ich, wie das abläuft: Wenn Arnaud Chastaignt seine ästhetische Idee mitgeteilt hat, wird ein Projektteam gebildet. Bei der Arbeit an der Hyper Cybernetic, die sich durch harte Übergänge von Weiß zu Schwarz auszeichnet, erkannte das Technische Büro, dass anders gebaut werden musste als geplant. Die Uhr besteht aus zwei „halben“ Hauben, die an der Schnittkante so zusammengebracht werden müssen, dass die Uhr wasserdicht ist und alle üblichen internen Tests besteht. Die Entwicklungsabteilung entschied sich für einen metallenen Ring, der den Gehäusekern unter den Hauben bildet und so für die nötige Wasserdichtheit sorgt. Sobald das Technische Büro weiß, wie das Gehäuse genau aussehen muss, lässt es ein Wachsmodell anfertigen, um die ästhetische Freigabe von Chastaignt zu erhalten. Anschließend wird ein Prototyp erstellt.
Testen bis zum Limit
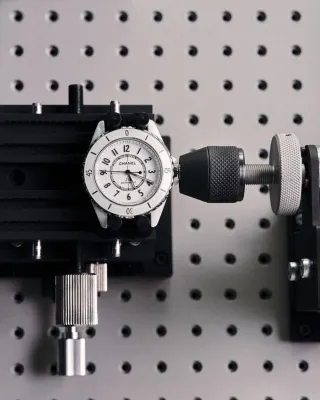
Inzwischen sind wir in der Testabteilung angekommen. Man merkt, dass sie bei Chanel sehr stolz auf diesen Bereich sind. Hier führt man alle möglichen Arten von Prüfungen durch: Uhren erhalten unterschiedliche Arten von Schlägen und Stößen, müssen verschiedensten klimatischen Bedingungen und extremen Temperaturwechseln trotzen. Hier werden Bänder gedehnt, gestreckt, gedreht und gerieben, was das Zeug hält, unter Zugabe von synthetischem Schweiß. Sie werden mit UV-Strahlung bombardiert, mit Parfums, Sonnencremes und Anti-Mücken-Sprays kontaminiert. Zu den Tests zählen auch die Überprüfung von Wasserdichtheit und Resistenz gegen Magnetfelder. Mit fällt so schnell kein Qualitätscheck ein, an den Chanel nicht gedacht hätte. Es werden Szenarien durchgespielt wie das Liegen am Strand oder der Transport in der Damenhandtasche. Für Ersteres wird eine Uhr im Sand verbuddelt und geschüttelt. Nach dem Herausnehmen wird sie gewaschen, und dann prüft man, ob sich die Lünette noch drehen lässt oder ob ein Sandkorn den Mechanismus blockiert. Für den Tropentest wiederum muss das Objekt 14 Tage lang 40 Grad Celsius und 90 Prozent Luftfeuchtigkeit aushalten, ohne danach Anzeichen von Korrosion zu zeigen. Insgesamt wird eine neue J12 rund 3.000 verschiedenen Tests unterzogen, das entspricht einer Dauer von 24.000 Stunden oder 1.000 Tagen.
Spezialisten für Keramik
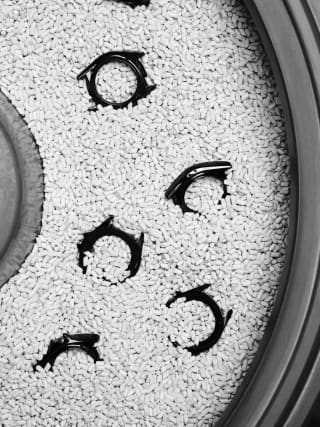
Die J12 überraschte bei ihrem Start 2000 nicht nur durch ihre Form, sondern vor allem durch ihr Material: polierte, glänzende Keramik. Das Material ist hart und kratzfest sowie antiallergen. Da Chanel sich gegen Metall und für Keramik entschied, konnte die Marke ihre typische Schwarz-Weiß-Optik in unverfälschter Form an die Uhr bringen. Zurzeit gibt es in der Schweiz nur drei Unternehmen, die Keramikgehäuseteile für Uhren fertigen: die zur Swatch Group gehörige Comadur, die unter anderem für Rado arbeitet; Rolex, die ihre eigenen Keramiklünetten herstellen; und eben G&F Châtelain. Nicht nur, weil es hier so laut ist, hängen wir an den Lippen von Olivier, dem Direktor des Keramik-Workshops. Er erklärt, dass der Herstellungsprozess in mehrere klar abgegrenzte Schritte aufgeteilt ist: Er beginnt mit der Auswahl des Ausgangsmaterials, das besonders rein sein muss. Die Keramik, die Chanel benutzt, ist Zirkoniumoxid. Dieses hat einen attraktiven Glanz und ist besonders hart, sodass eine Uhr aus diesem Werkstoff Jahrzehnte überleben kann. Auch breche eine J12 nicht gleich, wenn sie mal herunterfällt, sagt Olivier – anders als Porzellan, das sofort zerspringt. Zudem lasse sich Zirkoniumoxid mechanisch gut bearbeiten. Das Ausgangsmaterial kauft Chanel in Pulverform in Japan ein, weil dort die erfahrensten Lieferanten zu finden sind. Dabei geht es auch um die Farbe: Gerade beim Weiß hat Chanel, hat Arnaud Chastaignt klare Vorstellungen: Es darf nicht zu hell sein, kein „Weiß-Weiß“, sondern sollte einen warmen, leicht gelblichen Schimmer besitzen und einen gewissen Hauch an Transparenz mit sich bringen. Die exakte Farbe entsteht durch das Beimischen von Pigmenten; der genaue Prozess ist ein Geheimnis. Die gewünschte Rohform von Gehäusen, Lünetten oder Bandgliedern entsteht im Spritzgussverfahren: Dazu muss das Pulver zunächst weiterverarbeitet werden. Chanel kooperiert mit einem Lieferanten aus Deutschland, der sich darauf spezialisiert hat, das Keramikpulver mit dem richtigen Kunststoff-Bindemittel und den passenden Additiven zusammenzubringen und so das zum Spritzgießen benötigte Granulat zu erzeugen.
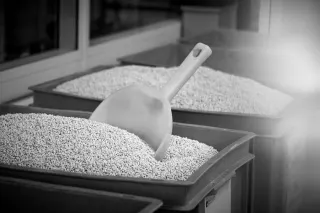
Nach dem Spritzgießen wird das beigemischte Kunststoff-Bindemittel im Wasserbad gelöst und herausgedampft, und dann kommt der entscheidende Akt: das Sintern. Das ist eine Art Backen in einem 1.300 bis 1.400 Grad heißen Sinterofen, das dazu dient, das nach dem Entzug des Bindemittels poröse Material zu härten, indem die einzelnen Partikel zusammengepresst werden. Nach dem Sintern ist das Teil nicht nur härter und um etwa 25 Prozent kleiner, auch die Farbe hat sich verändert und ist nun die endgültige. Jetzt ist das Gehäuse oder Bandglied fast fertig, aber es fehlt noch der letzte Feinschliff. Für diesen sind zwei weitere aufwendige Arbeitsgänge vonnöten. Zuerst wird die Silhouette des abgekühlten Teils in mehreren Arbeitsgängen maschinell geschliffen, damit es bereits einigermaßen glatt wird. Dafür benötigt man Spezialwerkzeuge, denn die gesinterte Keramik ist etwa siebenmal härter als Stahl. Abschließend erfolgt in einem mit Poliernuggets gefüllten Rüttelbehälter die Politur. Dieser letzte Schritt ist noch einmal ein ganz entscheidender Prozess, in dem die Oberflächen das erhalten, was die Keramik neben ihrer Härte und Wärme optisch wie haptisch ausmacht: ihre extreme Glätte und den unverwechselbaren Glanz.
Steinesetzen ist Handarbeit
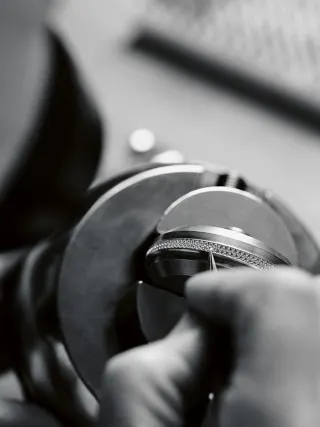
Diamanten spielen bei Chanel-Uhren eine große Rolle. Das beginnt bei den J12-Damenuhren, bei denen Diamanten als Stundenindexe fungieren, und geht bis zu superexklusiven Limited Editions wie der voll ausgefassten J12 Kaliber 12.1, die nur 20-mal gefertigt wird. Um höchste Qualität zu gewährleisten, werden bei Chanel alle Steine von Hand gesetzt. Victor, der Leiter der 19-köpfigen Abteilung, erklärt uns die drei Qualitätsstufen in der Produktion: Beim „mechanisch vorbereiteten Steinsetzen“ werden die Vertiefungen, in die später die Steine gesetzt werden, durch Maschinen eingebracht. Beim traditionellen Steinesetzen dagegen, der zweiten Stufe, schaffen die Mitarbeiterinnen und Mitarbeiter (das Verhältnis zwischen Männern und Frauen ist etwa 50 zu 50) diese Vertiefungen ausnahmslos durch Gravieren von Hand – ein Prozess, der bis zu 45 Stunden dauern kann. Die höchste Qualitätsstufe bildet schließlich das sogenannte „gehämmerte Steinesetzen“: Hier wird zunächst jeder Stein speziell für das Teil, auf das er gesetzt wird, geschnitten, sodass er dessen Form perfekt folgt. Anschließend wird das umgebende Material, also Stahl oder Gold, an den Rändern so umgebogen, dass es die Diamanten oder Rubine festhält. Damit entfallen traditionelle Fassungen.
Komponentenfertigung
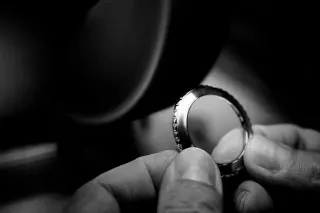
Im Atelier für Teilefertigung werden unterschiedlichste Komponenten für Werke, Gehäuse und Armbänder gefertigt. Hier ist es so laut, dass man den Guide kaum versteht, aber was man sieht, kennt man von anderen Produktionsstätten der Uhrenindustrie: CNC-, Stanz- und Drehmaschinen sowie Apparaturen für Elektroerosion verwandeln Rohteile aus Stahl und Messing, Gold und Titan in Lünetten, Bandglieder und andere Uhrenbestandteile. Auch das Bearbeiten von Oberflächen wie Polieren und Sandstrahlen steht auf dem Programm. Nicht alles geschieht dabei in Eigenregie: Kronen, Zeiger, Zifferblätter und Schrauben kauft Chanel zu, PVD-Beschichtungen und das Goldplattieren werden außer Haus gegeben. Doch insgesamt entstehen nicht weniger als 70 Prozent aller verwendeten Chanel-Uhrengehäuse hier, bei den Bändern liegt der Anteil noch weit darüber.
Montage
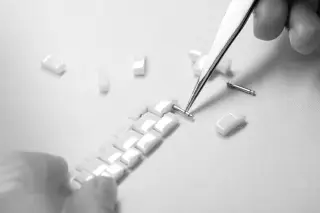
Die Chanel-Manufaktur besitzt drei verschiedene Montage-Workshops: einen für Armbänder, einen für Gehäuse und einen für den Zusammenbau der Uhren. Dass ein Uhrenhersteller seine Bänder selbst montiert, ist die Ausnahme, entsprechend selten sieht man das. Und auch hier erfahre ich wieder Spannendes, nämlich dass ein Chanel-Gliederband aus ungefähr 90 einzelnen Teilen besteht. Die Uhrenmontage findet in Reinraumatmosphäre statt, daher dürfen wir sie nicht betreten, damit nicht zu viel Staub und andere Partikel von der Straße hineingelangen. Je nach Modell braucht es fünf bis sechs Fertigungsschritte, bis der Uhrenkopf vollendet ist, danach wird das Band befestigt und zur Endkontrolle geschickt.
Haute Horlogerie
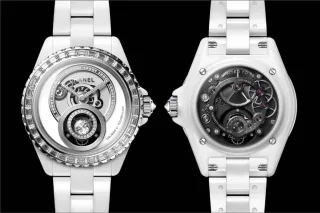
Für die Komplikationsuhren hat Chanel eine eigene Abteilung eingerichtet: das Atelier Haute Horlogerie. Diese Uhren, die in kleinen Stückzahlen entstehen, werden jeweils von ein und demselben Uhrmacher beziehungsweise derselben Uhrmacherin von A bis Z zusammengebaut. Auch am Beginn der Entwicklung jedes dieser Uhrwerke steht eine kreative Idee von Arnaud Chastaignt. An einem Beispiel lässt sich veranschaulichen, wie der Prozess läuft: Chastaignt sah für das Kaliber 5 ein fliegendes Tourbillon mit einem Diamanten im Zentrum vor, der sich im Sekundentakt dreht, umgeben von einem Ring aus 26 kleineren Diamanten. Die Vorschläge des Technischen Büros aus La Chaux-de-Fonds lehnte er zweimal ab, weil ihm der Diamant in beiden Fällen nicht groß genug war. Erst als die Planung den Durchmesser auf 4,5 Millimeter brachte, gab er grünes Licht. Diese Größe schuf aber für die Verantwortlichen in der Manufaktur ein neues Problem, denn so ein großer Diamant wäre zu dick für seinen Platz im Werk gewesen. So entwickelte die Abteilung eine neue, dünnere Form. Eine Abwandlung des Kalibers 5 ist das Kaliber 5.1 in der Monsieur de Chanel Tourbillon Meteorite: Hier hat der Chanel-Löwe den Diamanten ersetzt.
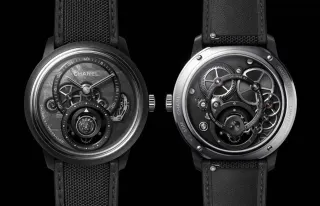
Insgesamt hat Chanel in den letzten sieben Jahren für seine Komplikationsuhren fünf Kaliberfamilien entwickelt, aus denen 25 Kaliberversionen entstanden sind. Für das Kaliber 1 mit Handaufzug, springender Stunde und retrograder Minute kooperierte man zum Start 2016 noch mit dem unabhängigen Uhrmacher Romain Gauthier, die eigentliche Konstruktion erfolgte aber bei Chanel. 2017 folgte für die Linie Première das skelettierte Damenkaliber 2, dessen Brücken die Form einer Kamelie ergeben, der Lieblingsblume von Coco Chanel. 2018 sah die Einführung des gleichfalls skelettierten Kalibers 3 mit kreisförmigen Brücken im Modell Boyfriend. Wie bei den einfacheren Modellen spielt die Beachtung der Chanel-Designcodes auch bei den Haute-Horlogerie-Uhren eine wichtige Rolle. Bei jedem Modell finden sich zwingend irgendwo der oben erwähnte Löwenkopf sowie ein Kreis im Kreis. Großen Wert legt Chanel darüber hinaus auf die Finissierungen: Flache, spiegelpolierte Schrauben und Zahnräder, diamantanglierte Kanten und gewölbte Steine dienen dazu, das Licht stark zu reflektieren, während es kreisförmig satinierte Oberflächen und schwarze ADLC- Beschichtungen (ADLC = engl.: amorph diamond-like carbon) im Gegensatz dazu eher schlucken. Skelettierte Brücken sorgen wiederum dafür, dass man von außen so viel wie möglich von den Veredelungen im Innern des Werks sieht.Nach dem Besuch sah ich, dass ich mir über 20 Seiten Notizen gemacht hatte. Ich war mit der Erwartungshaltung gekommen, vor allem die Fertigung der Keramikgehäuse und -bänder zu erleben, und hatte dann so viel mehr gesehen: eine voll vertikalisierte Uhrenmanufaktur, die so viel einzigartiges Können unter ihrem Dach vereint. Für die Zukunft ist die Uhrensparte von Chanel gut aufgestellt. bucDieser Artikel erschien zuerst im Magazin Chronos, die aktuelle Ausgabe können Sie hier bestellen:)